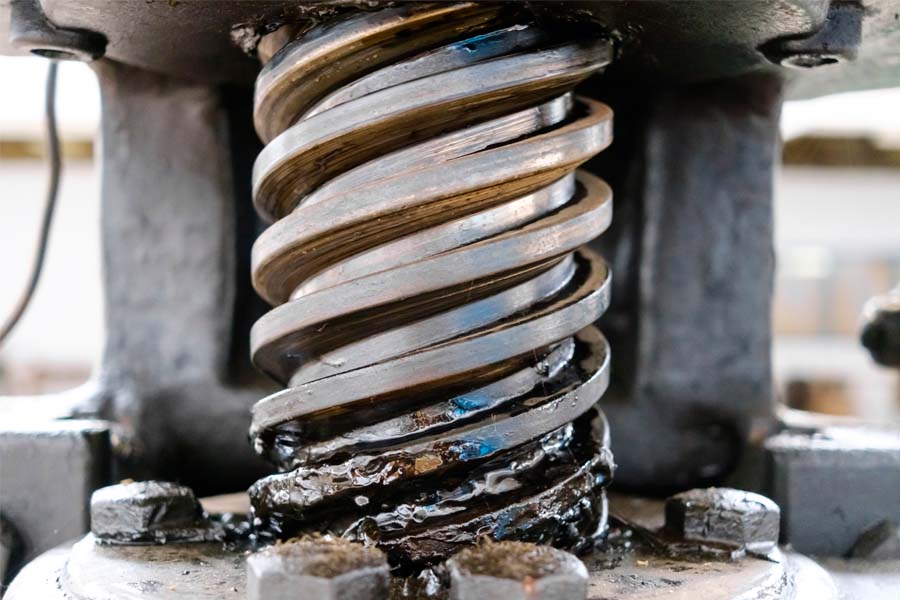
No mundo industrial moderno, a lubrificação adequada é essencial para garantir o funcionamento suave, eficiente e seguro de máquinas e equipamentos. A escolha do lubrificante correto pode fazer a diferença entre uma operação bem-sucedida e uma falha catastrófica.
Enquanto as graxas convencionais atendem a muitas necessidades básicas, elas podem não ser suficientes para aplicações que envolvem condições extremas ou requisitos específicos.
É aqui que entram as graxas especiais, formuladas para enfrentar desafios únicos e proporcionar proteção e desempenho superiores.
O que são Graxas Especiais?
Graxas especiais são lubrificantes avançados desenvolvidos com formulações exclusivas para atender a necessidades específicas que vão além das capacidades das graxas convencionais.
Elas combinam bases de óleo de alta qualidade com aditivos especiais e espessantes inovadores para oferecer propriedades excepcionais, como resistência a temperaturas extremas, pressões elevadas, ambientes corrosivos, entre outros desafios industriais.
Essas graxas são projetadas para prolongar a vida útil dos equipamentos, melhorar a eficiência operacional e reduzir os custos de manutenção a longo prazo.
Principais Tipos de Graxas Especiais e Suas Aplicações
1. Graxas de Alta Temperatura
As graxas de alta temperatura são essenciais para equipamentos que operam em ambientes com temperaturas elevadas, que podem ultrapassar 200°C. Em aplicações como fornos industriais, motores de alto desempenho, sistemas de exaustão e turbinas, a temperatura elevada pode causar a oxidação rápida e a degradação das graxas comuns.
As graxas de alta temperatura são formuladas com óleos base sintéticos e espessantes especiais, como complexos de sulfonato de cálcio ou poliureia, que resistem à oxidação e mantêm a estabilidade térmica. Isso evita a formação de depósitos, reduz o desgaste e garante uma lubrificação eficaz mesmo sob calor intenso.
2. Graxas de Baixa Temperatura
Em ambientes com temperaturas extremamente baixas, como regiões árticas ou câmaras frigoríficas, as graxas convencionais podem endurecer e perder sua fluidez, levando ao aumento do atrito e desgaste prematuro dos componentes.
As graxas de baixa temperatura são projetadas para permanecerem fluídas e eficazes em temperaturas que podem chegar a -50°C ou menos. Elas utilizam óleos base sintéticos de baixa viscosidade e aditivos que mantêm a flexibilidade, garantindo que os equipamentos iniciem e operem sem problemas em condições de frio extremo.
3. Graxas de Pressão Extrema (EP)
Equipamentos que operam sob cargas pesadas e choques mecânicos, como engrenagens industriais, rolamentos de grande porte e prensas, exigem lubrificantes capazes de suportar essas condições sem perder a eficácia. As graxas de pressão extrema (EP) contêm aditivos especiais, como compostos de enxofre-fósforo, que formam uma película protetora nas superfícies metálicas.
Essa película previne o contato direto metal-metal, reduzindo o desgaste e prevenindo a solda por fricção. Além disso, essas graxas ajudam a dissipar o calor gerado pelas cargas elevadas, contribuindo para a longevidade dos componentes.
4. Graxas Resistentes à Água
A presença de água em sistemas mecânicos pode levar à corrosão, à lavagem do lubrificante e à falha prematura dos componentes. As graxas resistentes à água são formuladas para repelir a água e manter suas propriedades lubrificantes mesmo em ambientes úmidos ou submersos. Elas utilizam espessantes como complexo de alumínio ou sulfonato de cálcio, que proporcionam excelente aderência e resistência à lavagem por água.
Essas graxas são ideais para aplicações marítimas, bombas submersas, equipamentos de processamento de alimentos e qualquer ambiente onde a exposição à água é significativa.
5. Graxas Alimentícias (Grau Alimentício)
Na indústria alimentícia e de bebidas, a segurança e a higiene são de suma importância. Equipamentos que entram em contato com alimentos exigem lubrificantes que não contaminem os produtos finais. As graxas alimentícias são formuladas com componentes atóxicos aprovados pelas agências reguladoras, como a FDA (Food and Drug Administration) e a NSF (National Sanitation Foundation).
Elas são usadas em rolamentos, engrenagens e outros componentes onde há risco de contato incidental com alimentos. Além de serem seguras, essas graxas também oferecem excelente desempenho em termos de lubrificação e proteção contra desgaste e corrosão.
6. Graxas Condutoras
As aplicações elétricas e eletrônicas requerem graxas que não apenas lubrificam, mas também conduzem eletricidade. As graxas condutoras são utilizadas em contatos elétricos, conectores e chaves, onde é essencial manter uma boa condutividade elétrica e proteger contra a corrosão. Elas contêm partículas metálicas finamente dispersas, como pó de prata ou cobre, que facilitam a passagem da corrente elétrica.
Além disso, essas graxas evitam a formação de óxidos nos contatos, garantindo a eficiência e a confiabilidade dos sistemas elétricos.
Benefícios do Uso de Graxas Especiais
Aumento da Vida Útil dos Equipamentos
O uso de graxas especiais adequadas às condições específicas de operação reduz significativamente o desgaste e a corrosão dos componentes mecânicos.
Ao proporcionar uma lubrificação eficiente sob condições extremas, essas graxas evitam falhas prematuras e prolongam a vida útil dos equipamentos. Isso resulta em menor necessidade de reparos e substituições, economizando tempo e recursos financeiros.
Eficiência Operacional
Equipamentos bem lubrificados operam de forma mais suave e eficiente, reduzindo o consumo de energia e aumentando a produtividade.
As graxas especiais minimizam o atrito e o calor gerado, permitindo que as máquinas funcionem em seu desempenho máximo. Além disso, a redução de paradas não programadas devido a falhas mecânicas melhora a confiabilidade das operações e cumpre os cronogramas de produção.
Segurança
Em setores críticos, como a indústria alimentícia, farmacêutica e aeroespacial, a segurança é primordial. O uso de graxas especiais certificadas garante que os produtos finais não sejam contaminados por substâncias nocivas.
Além disso, uma lubrificação adequada previne falhas mecânicas que poderiam levar a acidentes ou riscos operacionais, protegendo tanto os trabalhadores quanto os consumidores.
Economia de Energia
A redução do atrito entre as peças móveis através de uma lubrificação eficaz diminui o esforço necessário para operar os equipamentos.
Isso resulta em menor consumo de energia, reduzindo os custos operacionais e contribuindo para a sustentabilidade ambiental. Em larga escala, a economia de energia pode representar uma diminuição significativa da pegada de carbono da empresa.
Como Escolher a Graxa Especial Adequada
A seleção da graxa especial correta é um processo crítico que envolve vários fatores:
- Analisar as Condições Operacionais: Avaliar a temperatura de operação, pressão, velocidade, exposição a água, produtos químicos e outros fatores ambientais. Cada aplicação tem requisitos específicos que devem ser atendidos pela graxa.
- Consultar as Especificações do Fabricante: Os fabricantes de equipamentos geralmente fornecem recomendações sobre os lubrificantes adequados. Seguir essas diretrizes garante a compatibilidade e o desempenho ideal.
- Considerar a Compatibilidade de Materiais: Certificar-se de que a graxa não reagirá negativamente com os materiais dos componentes, como plásticos, elastômeros ou metais específicos.
- Testes e Monitoramento: Realizar testes em pequenas escalas ou em equipamentos menos críticos antes de uma implementação completa. Monitorar o desempenho da graxa ao longo do tempo para ajustar conforme necessário.
- Consultar Especialistas em Lubrificação: Profissionais com conhecimento técnico podem fornecer orientações valiosas na seleção da graxa adequada, considerando as nuances de cada aplicação.
O Papel Fundamental das Graxas Especiais na Eficiência Industrial
As graxas especiais são elementos essenciais na manutenção industrial moderna. Elas oferecem soluções personalizadas para desafios específicos, garantindo que os equipamentos operem com eficiência máxima, segurança e confiabilidade.
Investir em graxas especiais de alta qualidade não é apenas uma questão de manter as máquinas funcionando; é uma estratégia para otimizar operações, reduzir custos a longo prazo e obter vantagem competitiva no mercado.
A compreensão das necessidades específicas de cada aplicação e a seleção cuidadosa da graxa adequada podem resultar em benefícios significativos, incluindo maior produtividade, economia de energia e redução do impacto ambiental.
Empresas que adotam práticas avançadas de lubrificação estão melhor posicionadas para enfrentar os desafios atuais e futuros da indústria.